Rapid Glass Fiber Mesh
Rapid Glass Fiber Mesh has high strength, low elongation, high elasticity and rigidity, large shock resistance, good chemical resistance, low water absorption and high heat resistance. Alkali-resistant fiberglass mesh has excellent properties including water resistance, alkali resistance, flexibility, softness and resistance to aging. It is widely used in reinforcing walls, natural marble, plaster board, artificial stone materials and exterior insulation finishing materials.
* Sizes &Specification:
1) 45gsm – 100mm*50m
5mm*5mm – 150mm*50m
– 300mm*50m
– 1000mm*50m
2) 80 &110gsm – 100mm*50m
5mm*5mm – 150mm*50m
– 300mm*50m
– 1000mm*50m
3) 145gsm – 100mm*50m
5mm*5mm – 150mm*50m
– 1000mm*50m
4) 145gsm
10mm*10mm – 500mm*50m
– 1000mm*50m
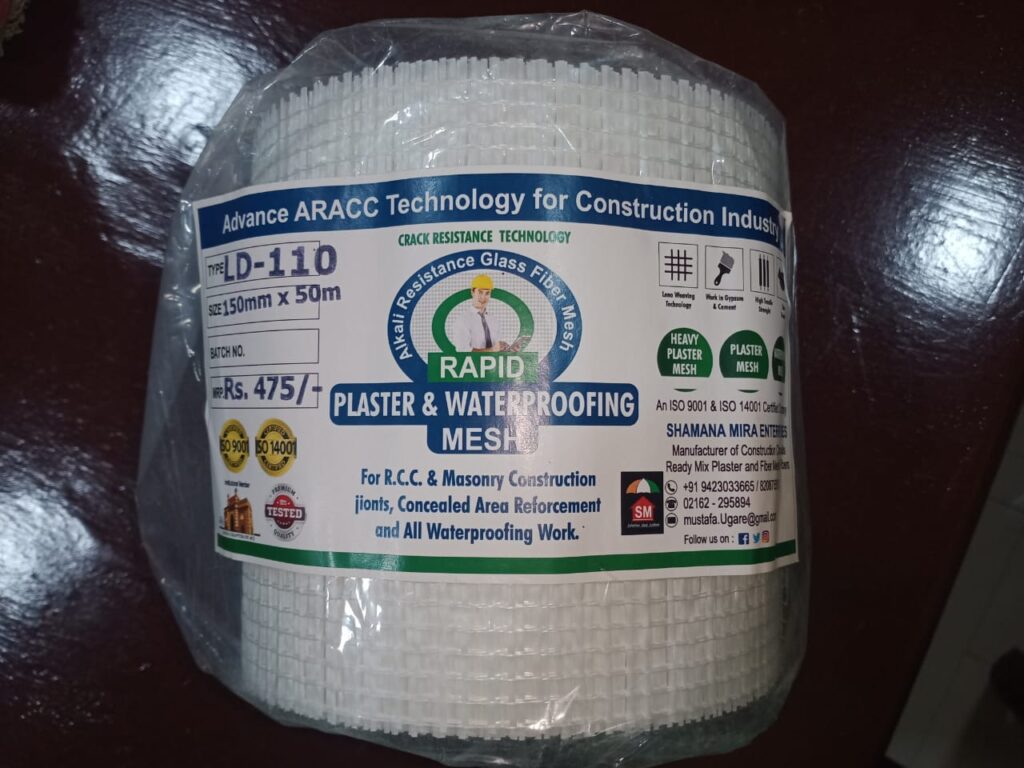
Rapid Tile Spacers
Tile spacer is specially designed to create a uniform gap between tiles, this results in proper alignment throughout the tiling area. The spacers are available in different width sizes starting from 2mm width to 10 mm width.
Features & Benifits
-
Spacers accommodate the movements due to thermal variations and different loads
-
When filled with the right grout material, they can efficiently reduce the free water flow / leakage through the joints and also make the joints anti fungal and anti bacterial
-
With spacers, we can create uniform designs and pattern
-
Improved aesthetics and dimensional stability to the entire tile/ stone assembly
-
It ensures longer life span of tile installation
Product Details
Applications: To create uniform spacing between tiles/stones resulting in an aesthetic and functionally stable tile/ stone assembly. Spacer sizes : 2 mm, 3 mm, 4 mm, 5 mm , 6 mm, 8 mm &10 mm.
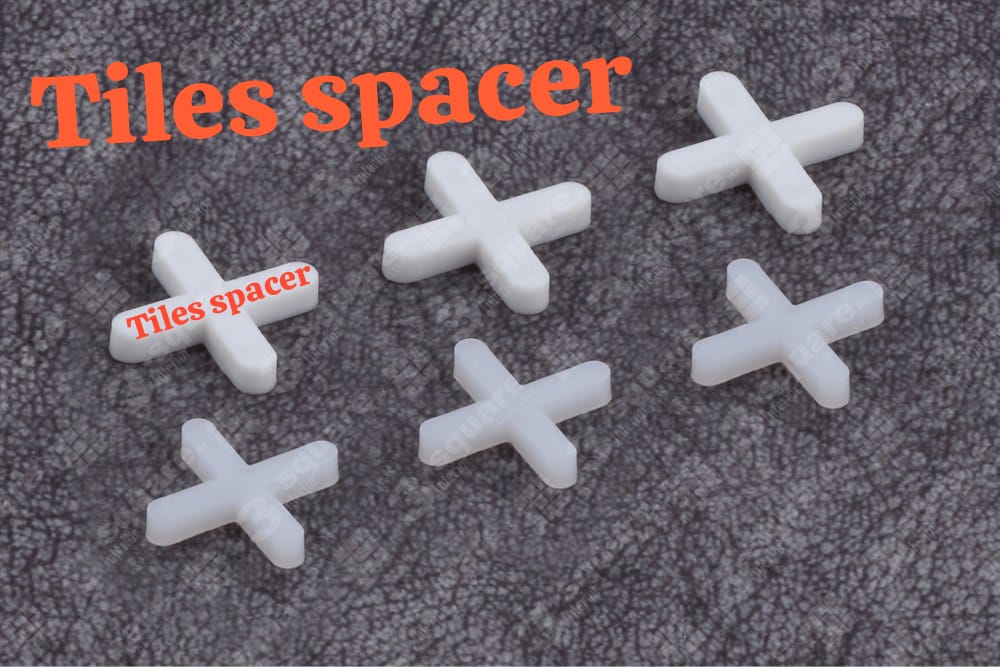
Rapid Tile Leveling Clips & Wages
The levelling Clips & Wedges is designed for a faster and easier tile installation. Easy to operate, it enables to obtain perfectly flat floor and wall coverings, even in the most difficult cases, such as the installation of large format slabs. Just two components and one simple movement are enough to quickly and accurately prevent lippage between adjacent tiles. Additionally, no need to use spacers to create grout lines.
Features & Benefits
- Compatible with all types of tiles.
- Fast installation time.
- Save money from costly repair.
Product Details
Applications: For all kind of tiles and stone slabs on floors and walls. Particularly suitable when installing large format tiles. For tiles with thickness from 3 to 12 mm. Packaging : Wedges & Clips – 3 mm & 4 mm.
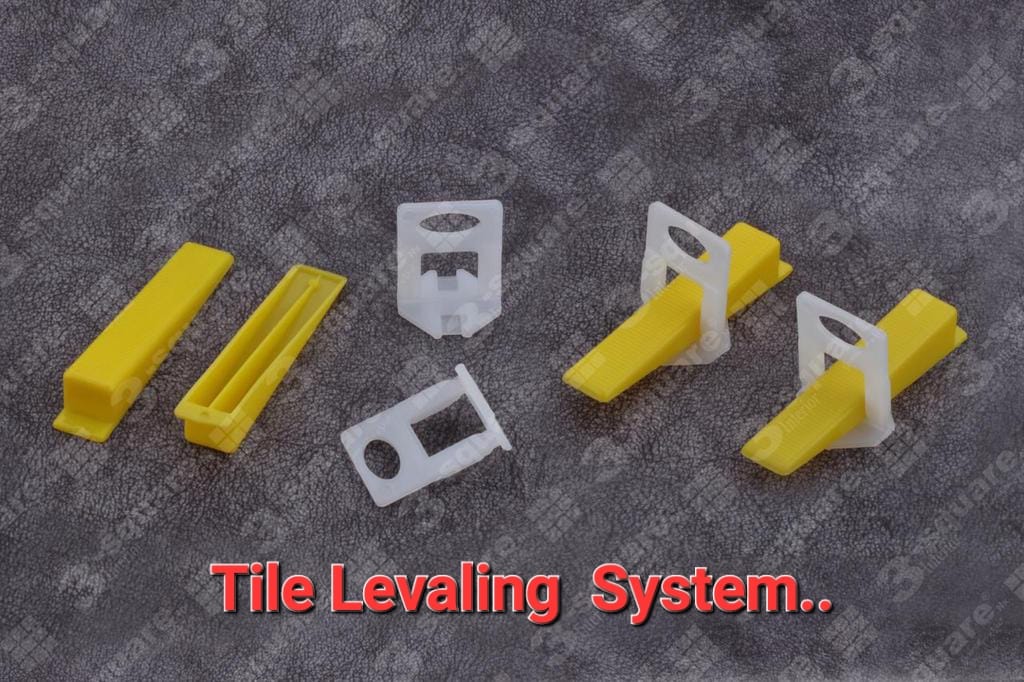
Rapid Readymix Plaster
Rapid Ready Mix plaster is a premixed ready to use cement based mortar for external as well as internal plaster, which ensures quality consistency. Rapid Ready Plaster is a single component water resistance monolithic plastering/rendering mortar with a ratio of graded sand, cement and polymers for applications in civil construction works.
Good plastering material and plaster should be capable enough to protect the wall from external UV rays, dampness, shocks, rain, humidity, fire and sound. It also gives thermal insulation to entire building. Good plastering work with good plastering material is the skin of entire building and provides long term durability to the building. Care should be taken to choose the right material for plastering. Effectiveness of plastering depends on material, workmanship, skill level of mason and adherence to general guidelines of its usage. Workability of mix, particle size distribution of material, control to avoid early heat of hydration, raw mix design, quality of individual raw materials is important. Sand used in plaster should have minimum clay content and other impurities. Control over maximum particle size and grading. Shape of sand is also a factor. Pozzolana used in material should have proper lime reactivity with control over other physical and chemical parameters. GGBS is used in Rapid Ready plast to control the early heat of hydration of mix to avoid cracking. Rapid Ready plast can be applied on Clay/Brick, Concrete block, AAC Block, Fly ash block and Concrete surface.
Features & Benefits of Rapid Readymix Plaster
- High compressive Strength -High Compressive strength increases masonry strength and load bearing capacity.
- Consistency -Due to the manufacturing process and accurate particle size distribution, the premix bags are delivered in consistent and best quality.
- No bulking of Sand -Conventional sand can be bulked by adding water and volume/weight of sand can be cheated. Sand used for making Ready mix plaster should be completely dry
- Saves Time -Huge time saving can be observed for plaster work and completion of project. There is no need to stack and mix individual materials like cement and sand.
- Hassle Free -No hassle of maintaining mortar ratio, whereas in the conventional method labour and supervision is required to prepare the mix.
- Easy Application -The material is premixed and only water has to be added on site. This makes the process of plastering much easier and quicker
- Minimum Wastage -The wastage caused in the conventional site mix process while sand sieving and mixing material is totally avoided.
- Minimum Cracks -Shrinkage cracks are minimized as raw materials are tested and accurately mixed with specific particle size and quantity.
- Storage -Easy to maintain stock as equal size packaging in bag form is provided.
- Higher Coverage -Due to lower density and high volume, it covers 15-22 sq ft/ bag of 40 Kg with a thickness of 10-12 mm
- Finish -Surface finish after application is excellent and equal due to best particle size grading, hence maximizing wall plaster performance.
- Economical -It provides smooth finish of walls in a single coat. Hence saves time and cost required for putty coating on inner wall and primer on external wall.
- Availability -Unlike the unstable availability of raw river sand, premix bags are available round the year.
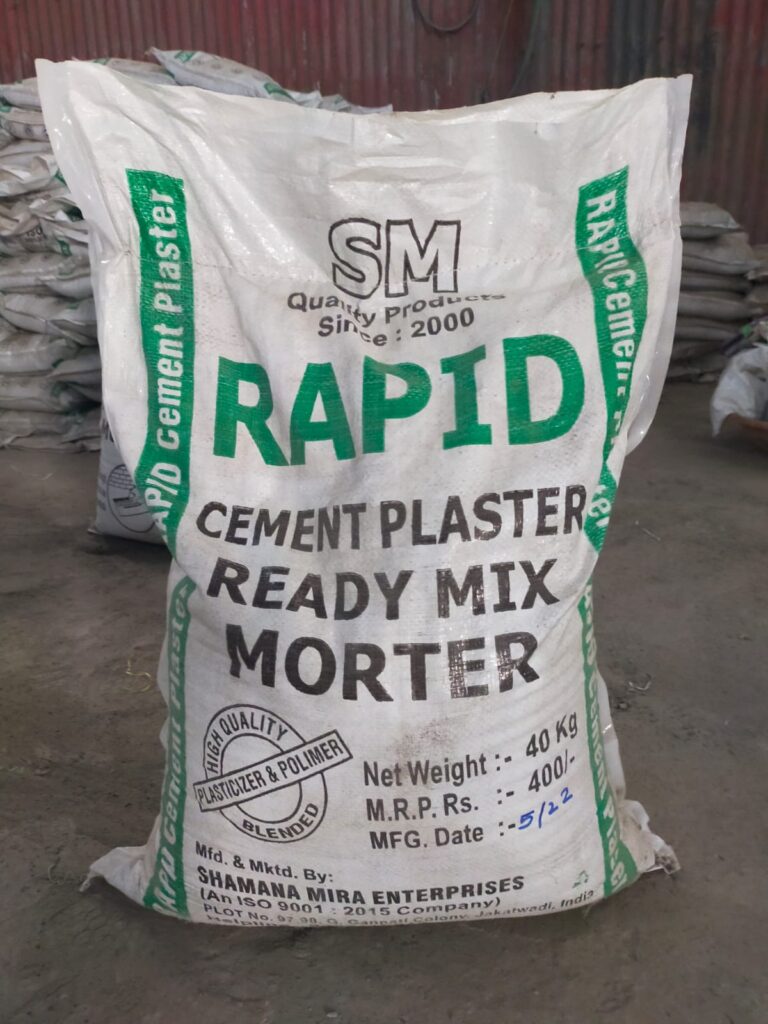
Rapid Construction Fiber
Rapid acts as “secondary reinforcement” in concrete which arrests cracks, increases resistance to impact/abrasion & greatly improves quality of construction in walls, foundations, tanks, roads and pre-cast products like blocks, pipes, tiles, manhole covers, and more. Reliance Industries Limited brings your Rapid. The new generation fibre used in a variety of significant industrial applications such as paper, asbestos cement products, construction and lead acid battery.
Rapid virgin polypropylene fiber
- To be mixed in cement to develop crack free structure
- Standard mix:1 pouch per cement bag (50kgs)
- Uses: Slabs Beams Columns Flooring Wall plastering RCC & PCC lintels Tiles Roads and pavements
- Advantages: Crack free structure Reduces rebound loss by 50-70%Work gets completed faster Protects steel from corrosion
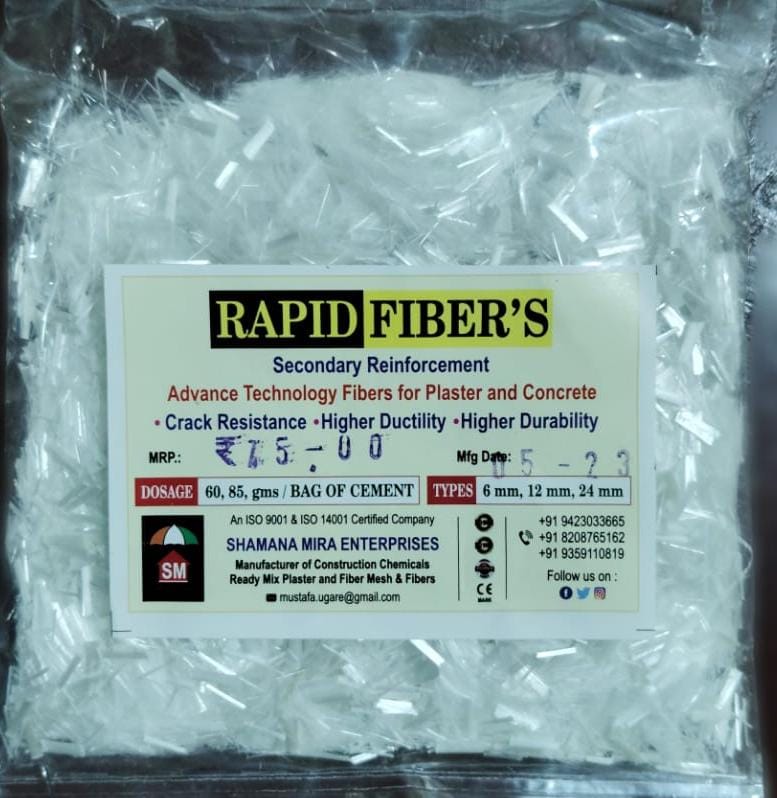
AAC Blocks
All You Need To Know About Autoclaved Aerated Concrete (AAC) Blocks
If you want to build a house while being environmentally conscious, AAC blocks are the way to go. Autoclaved Aerated Concrete (AAC) is a certified green building material that is lightweight, load-bearing, high-insulating, durable, and three times lighter than red bricks.
SHARE:
AAC blocks were invented by a Swedish architect in November 1924, who was looking for a building material that would resist decay, combustibility, and termites. In this article, we are going to discuss different types of AAC blocks and their advantages and disadvantages.
What Are AAC Blocks ?
Autoclaved Aerated Concrete (AAC) block is a low-maintenance precast building material with excellent thermal insulation and durability. The heat-insulating properties of AAC blocks keep the building cooler and prevent outside heat from entering, resulting in significant savings on air conditioning costs. AAC blocks also guarantee savings in foundation load, structural steel consumption, and mortar consumption.
Types of AAC Blocks
1)Fire Resistant AAC Blocks
2)200 Mm AAC Block
3)100 mm AAC Block
4)Long-lasting AAC Block
5)Rectangular Fly Ash AAC Blocks
Advantages Of AAC Blocks
1)Easy & Faster Workability :
AAC blocks are about half the weight and ten times the size of traditional bricks. This one-of-a-kind property allows for simple installation and provides the desired flexibility, making adjustments, cutting, shaping, and so on a breeze. AAC blocks have fewer joints and consistent dimensions, making them easier to lay and the construction process faster. Finally, lightweight blocks are easy to transport, which helps to reduce overall logistics and shipping costs when compared to traditional brick transportation costs.
2)Disaster Resistant :
Self-weight and gravity are usually the two vertical forces that a building is designed to handle. Earthquakes, for example, cause horizontal forces. As a result of the manufacturing process, AAC blocks become extremely strong, resulting in a durable finished structure. In comparison to conventional bricks, AAC bricks can handle higher seismic loads.
3)Thermal Insulation And Energy Conservation :
By foaming the concrete with hydrogen, the material provides excellent heat insulation, allowing temperatures to be warm in winter and cool in summer. Thus, it can reduce your air-conditioning costs by about 25%. Due to their energy-efficient production, AAC blocks are energy-efficient throughout their lifetimes.
4)Soundproof :
Because AAC blocks are lightweight and porous, they reduce sound significantly. It is for these reasons that AAC blocks are widely used in the construction of studios, hospitals, hotels, etc.
5)Sustainable And Pocket-Friendly :
AAC blocks are produced with a minimum amount of waste using natural, non-toxic raw materials. Some of the waste or offcuts produced can be recycled or used to make aggregates. Its use of non-biodegradable materials makes the building more durable and steady, preventing rot and mould. Furthermore, because AAC blocks are lightweight, energy-efficient, and simple to install, they reduce labour costs.
6)Fire Resistance :
Comparatively to other building materials, AAC blocks are non combustible and provide fire resistance of up to six hours, depending on their thickness and up to 1,200 degrees Celsius. Therefore, it has also significant fire safety implications.
7)Moisture Proof :
Moisture can cause significant structural damage. The macro-pores within AAC blocks ensure low water absorption. As a result, they offer better moisture protection.
Disadvantages Of AAC Blocks
- – Due to their brittle nature, AAC blocks demand greater caution when handling and transporting than clay red brick. AAC blocks are expensive per unit, but overall masonry costs are low because less cement mortar is used during installation.
- – Because AAC blocks are brittle by nature, they can break readily. It is fragile by nature because of the spaces.
- – They have a very high water absorption rate. This causes fissures in the structure as a result of their expansion when water is absorbed and contraction when moisture is lost.
- – Interior finishes must have low vapour permeability and exterior finishes must have high permeability when installed in high-humidity settings
AAC BLOCKS
All You Need To Know About Autoclaved Aerated Concrete (AAC) Blocks
If you want to build a house while being environmentally conscious, AAC blocks are the way to go. Autoclaved Aerated Concrete (AAC) is a certified green building material that is lightweight, load-bearing, high-insulating, durable, and three times lighter than red bricks.
Share:
AAC blocks were invented by a Swedish architect in November 1924, who was looking for a building material that would resist decay, combustibility, and termites. In this article, we are going to discuss different types of AAC blocks and their advantages and disadvantages.
What Are AAC Blocks ?
Autoclaved Aerated Concrete (AAC) block is a low-maintenance precast building material with excellent thermal insulation and durability. The heat-insulating properties of AAC blocks keep the building cooler and prevent outside heat from entering, resulting in significant savings on air conditioning costs. AAC blocks also guarantee savings in foundation load, structural steel consumption, and mortar consumption.
Types Of AAC Blocks
1)Fire Resistant AAC Blocks
2)200 Mm AAC Block
3)100 mm AAC Block
4)Long-lasting AAC Block
5)Rectangular Fly Ash AAC Blocks
Advantages Of AAC Blocks
1)Easy & Faster Workability :
AAC blocks are about half the weight and ten times the size of traditional bricks. This one-of-a-kind property allows for simple installation and provides the desired flexibility, making adjustments, cutting, shaping, and so on a breeze. AAC blocks have fewer joints and consistent dimensions, making them easier to lay and the construction process faster. Finally, lightweight blocks are easy to transport, which helps to reduce overall logistics and shipping costs when compared to traditional brick transportation costs.
2)Disaster Resistant :
Self-weight and gravity are usually the two vertical forces that a building is designed to handle. Earthquakes, for example, cause horizontal forces. As a result of the manufacturing process, AAC blocks become extremely strong, resulting in a durable finished structure. In comparison to conventional bricks, AAC bricks can handle higher seismic loads.
3)Thermal Insulation And Energy Conservation :
By foaming the concrete with hydrogen, the material provides excellent heat insulation, allowing temperatures to be warm in winter and cool in summer. Thus, it can reduce your air-conditioning costs by about 25%. Due to their energy-efficient production, AAC blocks are energy-efficient throughout their lifetimes.
4)Soundproof :
Because AAC blocks are lightweight and porous, they reduce sound significantly. It is for these reasons that AAC blocks are widely used in the construction of studios, hospitals, hotels, etc.
5)Sustainable And Pocket-Friendly :
AAC blocks are produced with a minimum amount of waste using natural, non-toxic raw materials. Some of the waste or offcuts produced can be recycled or used to make aggregates. Its use of non-biodegradable materials makes the building more durable and steady, preventing rot and mould. Furthermore, because AAC blocks are lightweight, energy-efficient, and simple to install, they reduce labour costs.
6)Fire Resistance :
Comparatively to other building materials, AAC blocks are non combustible and provide fire resistance of up to six hours, depending on their thickness and up to 1,200 degrees Celsius. Therefore, it has also significant fire safety implications.
7)Moisture Proof :
Moisture can cause significant structural damage. The macro-pores within AAC blocks ensure low water absorption. As a result, they offer better moisture protection.
Disadvantages Of AAC Blocks
1)Due to their brittle nature, AAC blocks demand greater caution when handling and transporting than clay red brick. AAC blocks are expensive per unit, but overall masonry costs are low because less cement mortar is used during installation.
2) Because AAC blocks are brittle by nature, they can break readily. It is fragile by nature because of the spaces.
3)They have a very high water absorption rate. This causes fissures in the structure as a result of their expansion when water is absorbed and contraction when moisture is lost.
4) Interior finishes must have low vapour permeability and exterior finishes must have high permeability when installed in high-humidity settings
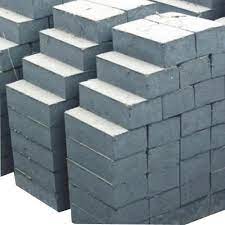
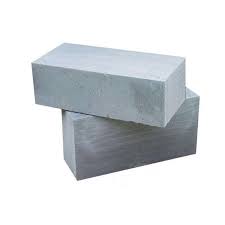